PROCESSING Ceramic forming processes may be classified as traditional - die pressing, cold isostatic pressing(CIP), slip casting and extrusion - or as new and emerging, such as injection moulding and tape casting. Some traditional methods have been refined or adapted to meet particular property requirements. These include hot isostatic pressing (HIP) and hot pressure.
With all forms of ceramic production, it is the aim of the manufacturer to ensure that flaws and defects are reduced at all stages of the process.
BOCHUANG CERAMIC has over 25 years experience in the development of engineering ceramic manufacturing processes to minimize defects in the sintered component and to ensure greater reliability in service. See followed main ceramic body shaping processing methods, we will accord customer application note then select suitable shaping technology
Die Pressing
This is by far the most widely used shaping technique for advanced ceramics and consists of the uniaxial compaction of a granular powder during confined compression in a die.
Injection Moulding In a similar manner to extrusion, a plastic mix is prepared and heated in the barrel of the moulding machine until it is at the correct temperature at which the mix has a sufficiently low viscosity to allow flow if pressure is applied. A plunger is pressed against the heated mixture forcing it through an orifice and on into the tool cavity. The moulded part is removed from the die and the organic binder slowly burnt out in a controlled atmosphere by means of a carefully controlled heating schedule, prior to sintering.
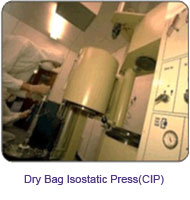 Cold Isostatic Pressing Granular powder or die pressed compacts are loaded into a flexible air-tight container, typically polyurethane, placed in a closed pressure vessel filled with liquid and compacted by increasing the pressure within the vessel. The pressure change takes place throughout the liquid, thus exerting a uniform applied pressure over the entire surface area of the air-tight container. In this way, the material is uniformly compacted and will retain the general shape of the flexible container, and any internal tooling profile.
Slip Casting
Slip casting refers to the filling of a mould, a negative of the desired shape, with a slip consisting of a suspension of micrometer size ceramic particles in liquid.
Tape Casting
This process involves the casting of a slurry onto a flat moving carrier surface. The slurry usually consists of a ceramic powder with the appropriate additions of solvents plasticisers and binders.
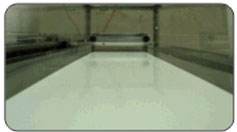 Doctor Blade on Tape Cast Strip "As-Cast" Strip
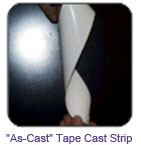
The slurry passes beneath the knife edge as the carrier surface advances along a supporting table. The solvents evaporate to leave a relatively dense flexible sheet that may be stored on rolls or stripped from the carrier in a continuous process.
Sintering or Firing
Once the ceramic powder has been compacted and green machined (if required) the "powder compact" is usually around 50% of its final theoretical density. Full densification is achieved by sintering at temperatures up to 1800°C.
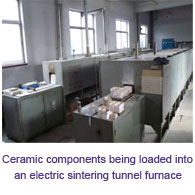
The sintering or firing process provides the energy to encourage the individual powder particles to bond or "sinter" together to remove the porosity present from the compaction stages. During the sintering process the "green compact" shrinks by around 40 vol %. However, this shrinkage is predictable and can be accommodated.
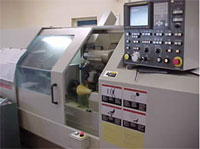 Diamond Grinding
High levels of accuracy and surface finish can be achieved by diamond grinding. Tolerances of a few microns are commonplace.
However, diamond grinding is a relatively expensive micro-machining process, consequently, if a design can be produced to "as-fired" tolerances, the overall cost of the component is reduced.
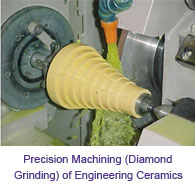
Green Machining
This technique is commonly applied to as-pressed parts which are still in a "chalky" condition. Common metalworking machines are used to machine the part in this "soft" condition as greater material removal rates are possible than by post sintering operations such as diamond grinding.
As fired green machined components are subject to maximum tolerances of +/- 1%. To achieve tighter tolerances diamond grinding must be employed.
For some special application of customers, we also could make the ceramic body use Hot Isostatic Pressing (HIP) process in third party( cooperated with some Institute), This technique involves sintering a compact at high temperature in a pressurised gas atmosphere. The compact must either be impermeable to the pressurising gas or be encapsulated in a gas-tight container. In the former case, powder compacts are first sintered to remove surface connected porosity.The use of hot isostatic pressing leads to additional densification and increased strength.
|